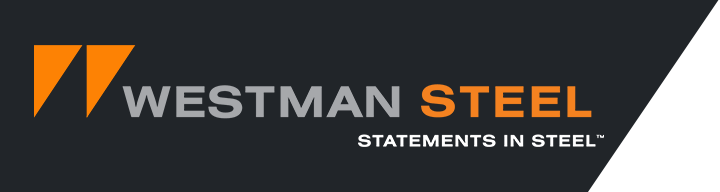
Edco Roofing
Preparation and General Conditions*Cartons should be stored in dry place under cover. Carry only one carton at a time and avoid having loose pieces on the roof.
- Follow all workers compensation and OSHA safety guidelines.
- Minimum recommended roof pitch is 4/12. Contact EDCO for recommendations on roofs less than 4/12 pitch.
- Inspect all roof sheathing and framing to make sure that it is free of warping, in good condition and fastened properly.
- When re-roofing determine if existing roofing needs to be removed. Before installing new shakes/slate over existing asphalt shingles, remove any mouldings on fascia board, cut back existing shingles flush with the fascia board at all roof edges and then install an underlayment.
- A Class ''A'' fire rating can be achieved by covering the entire roof area with an approved and tested fire resistant material such as Georgia-Pacific 1/4'' Dens-Deck or Elk VersaShield. The fire resistant material must be applied directly over the sheathing or existing roof and underneath the new underlayment. Shakes/slate installed directly over a synthetic underlayment or #30 felt underlayment without a fire resistant material will achieve a Class ''C'' fire rating.
- The entire roof must be covered with an underlayment prior to installing shakes/slate. The underlayment should be selected based on climatic weather conditions and must comply with all local building codes. A synthetic underlayment or #30 felt can be used with double layers at the eaves edge to a point at least 24'' inside the exterior wall line, 18'' on each side of the centerline along the entire length of the valley and around openings. The underlayments are to be overlapped according to manufacturer's recommendations and/or local building codes.
- In weather climates that experience freezing temperatures and high winds it would be advisable to use a high temperature, non granule coated polymer modified bitumen ice and water shield in lieu of the bottom layer of doubled underlayment and possibly throughout the entire job. High temperature ice and water shield is recommended for new construction as is following the manufacturer's recommendations. Follow local building codes.
- Proper attic ventilation is necessary. Using ArrowLine venting hip, ridge and soffit panels are an excellent way to ventilate the attic. See page 3 for details on preparing the roof and page 11 for installing the hip and ridge vents.
- When walking on roof always wear soft soled shoes or foam rubber soled overshoes and stay close to the top of the shake/slate just under the butt projection where the shake/slate is closest to under support. Always avoid walking on four way interlock of the shake/slate. Recommended scaffolding methods should always be adhered to.
- Architects, contractors, and roofing installers must ensure that construction bylaws and building codes are complied with and approved. Before construction begins, building permits may need to be obtained from the local building department. To qualify for protection under the manufacturer's warranty, the application instructions herein must be followed.
- Contact EDCO Products, Inc. for testing deails: UL 580-Uplift Resistance; UL 2218-Hail Resistance (4); FL4077-Florida Building Commission; CCMC 13380-R Canadian Construction Materials Centre, ICC ESR-3561.
- Use OSHA approved fall protection equipment when working on any roof.
* THIS INSTALLATION MANUAL IS INTENDED TO BE A GUIDELINE FOR INSTALLING OUR ARROWLINE ROOFING PRODUCTS, BUT DUE TO SPACE LIMITATIONS WE ARE ONLY SHOWING THE MORE COMMON WAYS TO APPLY THE ROOFING AND ACCESSORIES. THERE MAY BE MORE WAYS THAT ARE ACCEPTABLE THAT ARE NOT SHOWN HERE FOR INSTALLING THE ARROWLINE PRODUCTS. IF YOU HAVE ANY QUESTIONS PLEASE DISCUSS THEM WITH YOUR CONTRACTOR. EDCO PRODUCTS, INC. ASSUMES NO RESPONSIBILITY FOR LEAKS OR OTHER ROOFING DEFECTS DUE TO FAULTY APPLICATION. ARROWLINE ROOFING PRODUCTS ARE COVERED BY A LIFETIME LIMITED WARRANTY. FOR A COPY OF THE WARRANTY CALL 800 – 333 – 2580. OR YOUR LOCAL DEALER. USE A PROFESSIONAL CONTRACTOR FOR INSTALLATION OF YOUR ARROWLINE ROOF.
Shake/Slate installation sequence procedure
For new construction, it is recommended to use a high temperature, non-granule coated ice and water shield instead of #30 felt paper. The high temperature ice and water shield seals around screws and nails and is a final water barrier where there are conditions of heavy driving rain and ice dams. Refer to underlayment manufacturer's instructions and local building codes.
- Mount all eave starter trim (detail A - Page 4).
- Install 36'' wide high temperature, non granule coated ice and water shield at all eaves and valleys (denoted by dark lines & tint). 24'' beyond inside wall.
- Use high temperature, non-granule coated ice and water shield cut to 18-inch wide for end walls, vented and nonvented hips / ridges, skylights, rake edge, and any vents through the roof (denoted by tinted area).
- Cover the rest of the roof with ice and water shield, synthetic underlayment or #30 felt (denoted by white area). Follow local building codes.
- Install optional rake starter with 7/8'' j-trim ( Page 5).
- Install valley flashing (details C & D - Pages 6 & 7).
- Install end wall flashing (detail E - Page 8).
- Install roof panel going from left to right and bottom to top (detail F - Page 9).
- Install valley cap (Closed valley assembly - Page 7).
- Use 6-inch wide sub seal over unvented hips and unvented ridges. Mount vented and non-vented hip / ridge cap systems (details G & H - Pages 10 & 11).
General underlayment instructions
Tools needed
- Screw gun
- Hammer
- Chalk line
- Snips
- Caulk gun
- Roofing brackets or jacks
- Utility knife & blades
- Shingle remover
- Knee pads
- Portable brake
- Tape measure
- Hand seamer
- Hand stapler
Installing High temperature ice and water shield
Check to see that no nails or staples are protruding from the roof decking before applying high temperature, non granular coated ice and water shield. Do not nail any closer than 6'' from the rake edge or the bottom of the roof when mounting panels. Steps 2 & 3 are shown as tinted and Step 4 is shown as white.
2a: At the eave starter, apply the first row of 36'' underlayment to be flush to the bottom edge of the eave starter and flush at the gable ends. 24'' inside external wall.
2b: Install 36'' wide underlayment in valley (18'' each side with 6'' vertical overlap.)
3: Use underlayment cut to 18'' wide and provide 6'' of vertical overlap on hips, ridges, and rake edge.
4: Install 36'' wide ice and water shield on the entire roof with a minimum of 2'' horizontal lap and 4'' vertical lap if needed.
REFER TO LOCAL BUILDING CODESInstalling Synthetic underlayment or #30 felt paper
Check to see that no nails or staples are protruding from the roof decking before applying synthetic underlayment or #30 felt paper. Do not nail any closer than 6'' from the rake edge or the bottom of the roof when mounting panels. Steps 2 & 3 are shown as tinted and Step 4 is shown as white.
2a: At the eave starter, overhang the first row of 36'' wide underlayment to be flush to the bottom edge of the eave starter and flush at the gable ends.
2b: Install 36'' wide underlayment in valley (18'' each side with 6'' vertical overlap).
3: Use underlayment cut to 18'' wide and provide 6'' of vertical overlap on hips and ridges.
4: Install synthetic underlayment or #30 felt on the entire roof with a minimum of 2'' horizontal lap and 4'' vertical lap.
Eave Starter (Detail A).
Determine the roof pitch and bend the eave starter to the correct angle using a 10' brake. Install eave starter at all eaves. Fasten eave starter with #10 x 1'' long galvanized zip screws 12'' o.c. Screw length is to be long enough to penetrate the decking.
Underlayment is to be installed over the eave starter.
When installing roofing panels take care to avoid walking on the butt of the panels. It is recommended that you walk on the middle part of the panel. (See illustration to the right.)
Gable Edge (Detail B).
Install Eave Starter with 2'' of overlap going up the gable edge and over the underlayment. Fasten with #10 x 1'' galvanized zip screws. Cut a 7/8'' notch on both the bottom butt edge and top locking edge of the panel and extend it past the outer lip of the Eave Starter. This material will rolled over (or around) the Eave Starter. You can use the LT Rollover tool or a pair of wide-billed hand seamers to bend the 7/8'' notch down and around the lip of the Eave Starter.
Optional Gable Detail w/ J Trim
Have the panel overhang the eave starter by 7/8'' and cut to length. Notch the top and bottom legs of the shingle back 7/8''. Then form the shingle overhang around with LT Rollover Tool.
The optional Gable Detail with J Trim (shown above) is not recommended on roofs located in Snow Belt areas.
Open Valley Flashing (Detail C).
Regular Open Valley Installation
To assure a properly aligned and straight valley installation, it is important to first snap a chalk line in the center of the valley, running the full length of the valley. (Make sure underlayment has been applied in the valley per local building codes.) Then begin installing the valley flashing from the bottom. Trim the bottom of the valley to the correct angle and allow 5/8'' to bend around the eave starter. Notch hem of top valley and overlap valley 4'' and put 2 rows of sealant between overlap. Fasten valley in place with clips and fasteners on the outer edge of the valley every 16'' on center.
Remember to snip through the bottom clip and valley flashing so the valley flashing won’t down out of place. Next install the Open Valley Adjustable Starter. The Open Valley Adjustable Starter can placed either tight into the hemmed edge of the valley flashing or at another place that makes the open valley look portional. Fasten the Open Valley Adjustable Starter with #10 x 1'' screws spaced every 16'' on center. Always use sealant when overlapping accessories. (The roofing panels will need to be field hemmed to lock onto the Open Valley Adjustable Starter.)
Floating Valley Installation
To assure a properly aligned and straight valley installation, it is important to first snap a chalk line in the center of the valley, running the full length of the valley. Install Ice & Water Shield in the valley if needed. Run shake or slate panels up past the lowest point of the floating valley. Lay the valley flashing in the valley and over the panels coming up from below. Mark the valley so that it is long enough to drain any water out on top of the panel below. Trim and field form the valley as needed. Notch and lap the top of the valley if needed. Remember to apply two rows of sealant between the two pieces of valley at the lap. Fasten properly depending on which valley flashing you are using.
Closed Valley Assembly (Detail D).
To assure a properly aligned and straight valley installation, it is important to first snap a chalk line on the roof in the center of the valley, running the full length of the valley. Then begin installing the valley flashing starting from the bottom. Trim the bottom of the valley to the correct angle and allow 3/4'' to bend around eave starter. Notch hem of top valley and overlap valley 4'' and put 2 rows of sealant between overlap. Fasten valley using valley clips at 16'' o.c. Snip through clips on bottom of valley to hold it in place. Always use sealant when over-lapping accessories.
Use natural curing sealant on center of the flat top on the vee of the valley. Install the valley cap over the valley flashing flat top vee. The valley cap is installed with the lower always 2'' over the upper valley cap. Fasten using #8 x 1/2'' painted steel zip screws spaced 12'' o.c.
Note: In roof areas where you would have large volumes of snow or water running into the valley it may be advisable to use the Open Valley System. Also, in areas where leaves, needles and other debris might be a problem use the Valley Cap Filter Foam under the Valley Cap.
End Wall Flashing (Detail E).
The end wall flashing is designed to be used at the sides of end walls, dormers, chimneys, skylights, etc. Install ice & water shield cut to 18'' wide as counter flashing. Use matching embossed trim coil when custom top and bottom flashings are required. Always use proper sealants for water tightness.
Begin installing end wall flashing (always overlap trims by 4'' using sealant) with galvanized fasteners. In end wall applications, it is preferable to have the top leg of the end wall flashing go underneath the siding as far as possible. Use 6'' ice & water shield seal strip over the end wall flashing. When stucco or brick is present on end wall you must cut a kerf approximately 1/2” into the stucco or brick at least 4'' above the roof deck. Cut and bend end wall flashing to fit into kerf and allow for an edge to apply sealant.
When installing panels, cut a 3/4'' wide weep hole in the bottom butt edge of the panel inside the j-trim. This allows the end wall flashing to drain any moisture on top of the roofing panels.
Allow for proper drainage if chimney is in the middle of the roof. Check local building codes.
Shake/Slate Panel (Detail F).
After the completion of all prep work and the accessories have been applied, you can begin installing panels. Always install from left to right and attach with 5 clips per panel. The first and last clip on each course should be snipped at the hooking area through the top flange of clip. This procedure will help pin the course in place and minimize any horizontal shifting (see detail #1 below).
Start the installation at the bottom left hand corner of the roof with a full panel. After installing a number of panels you can start the second course. There are dimples stamped into the top hook of each panel. As noted above they have been designated ''1'', ''2'', ''3'' and ''4''. Do not start the second course with a full panel. In an effort to create a random staggered joint appearance it is recommended to cut the first shingleshake of the second course at dimple “2”. You may then continue installing on this course using only full panels. You can then begin the third course by cutting the first panel at dimple ''3'' and installing it. The fourth course should begin with a panel cut at dimple ''4''. The fifth course should be started with a full panel and you should repeat the above staggering procedure on all subsequent courses.
When installing at hips or valleys be sure to follow the above cutting procedure to insure the same random staggered pattern.
(When installing the panels be careful on where you walk on the panels. See page 4 for more information.)
SNOW DIVERTERS:
The use of snow diverters is recommended in areas where ice and snow can build-up on your roof.
The snow diverters should be installed and spaced according to the manufacturer's recommendations.
Hip / Ridge Assembly (Detail G).
Cut panels to the proper length and install as close to the hip or ridgeline as possible. Cover cut edges with 6'' of ice & water shield centered along the entire length of the hip or ridge edge. Bend Starter Base w/foam seal in a 10' brake to the correct roof pitch. Install starter base over the panels and overlap subsequent pieces approximately 4'' using sealant.
The hip / ridge caps should be installed over starter base with #10 x 1 1/2'' steel zip screws using 2 shingle clips per hip / ridge cap.
Hip / Ridge Assembly (Detail H). (Vented)
- When using the TrimLine vent system, first cut appropriately sized, 2'' wide venting opening through the roof decking to no closer than 6'' of the end walls. (See Ridge and Soffit Ventilation Requirements on p.12). When venting hips for more air flow, go down from the peak no more than 1/3 the maximum distance from the top. Going down the ridge too far effects air flow to the peak.
- Lay TrimLine vent with foam the full length of ridge, matching the pitch angle of the roof and keep straight. Tack and use sealant when necessary.
- Bend starter base to correct roof pitch over lapping 4'' on splices. Use #10 x 2'' steel zip screw spaced 12'' apart to keep the vent system as flat as possible.
- Install hip / ridge caps over the starter base with #10 x 2'' steel zip screws using 2 shingle clips per hip / ridge cap.
Ridge & Soffit Ventilation Requirements
Calculations are based on equal ventilation at the ridge and at the eaves. This requires a 1:300 ratio (1 square foot of ventilation to every 300 square feet of attic space). (Check the local building codebook for exact requirements.) This calculation is for 50% at the ridge and 50% at the soffit.
Note: The soffit and ridge vent are to be at least equal to each other. The eaves are recommended to have an adder of 10% to 25%, this increases airflow pressure to the peak.
Contact an architect or your local building official if you need additional information.
Calculations: using 5/8'' thick TrimLine Vent with 13 square inches / lineal foot of free air per foot.
- Calculate attic floor space 30 feet wide x 40 feet long = 1200 square feet
- Using 1:300 ratio net free airflow. (Total ridge and eave air flow) 1200 square feet / 300 square feet = 4 square feet
- Calculation for the ridge or soffits (50% min. for each) 4 square feet /2 = 2 square feet min.
- Convert 1 square foot to square inches for one side 144 square inches x 2 square feet (Total for ridge or soffit) = 288 square inches per side
- Trimline Vent Plus 5/8'' thick (13 sq. inches net free air per foot) used for ridge venting and hip venting 288 square inches / 13 = 22.15 feet of ridge vent
Attic Sq. Ft. | Sq. Inches at Ridge | Min. Ft. of Vent | Sq. Inches Soffit Vent |
---|---|---|---|
1000 | 240 | 18 | 240 |
1100 | 264 | 20 | 264 |
1200 | 288 | 22 | 288 |
1300 | 312 | 24 | 312 |
1400 | 336 | 26 | 336 |
1500 | 360 | 28 | 360 |
1600 | 384 | 30 | 384 |
1700 | 408 | 31 | 408 |
1800 | 432 | 33 | 432 |
1900 | 456 | 35 | 456 |
2000 | 480 | 37 | 480 |
2100 | 504 | 39 | 504 |
2200 | 528 | 41 | 528 |
2300 | 552 | 42 | 552 |
2400 | 576 | 44 | 576 |
2500 | 600 | 46 | 600 |
2600 | 624 | 48 | 624 |
2700 | 648 | 50 | 648 |
2800 | 672 | 52 | 672 |
2900 | 696 | 54 | 696 |
3000 | 720 | 56 | 720 |
Roof Vent Flashing
We recommend replacing all roof vents with the Trimline venting system (see page 11) . Do not mix TrimLine vents with other roof or gable vents . When using TrimLine vents remember to close off all other roof vents.
If individual roof vents are used to ventilate attic space, care should be taken in selecting an adequate number of properly sized roof vents . The vents should have metal flashing attached and all manufacturer's installation recommendations should be followed . The metal flashings on the vents should be reworked (as shown above) to assure a watertight installation . Use painted zip screws to install, along with sealant under flashing and on all sides of vent.
Pipe Vent Flashing.
Select properly sized vent pipe (a tight fit is important) with metal or rubber boot flashing. Follow manufacturer's installation guidelines and use adequate sealant to assure water tightness. Use painted zip screws to install, along with sealant under flashing and on all sides of vent.
Roof Jack
IMPORTANT: See hanger instructions from the manufacturer for proper use and mounting instructions required.
These instructions show modification of the roofing panel
- Mount hanger over top of panel per diagram.
- Mount top panel with clips.
- Remove hanger when done installing panels.
- Put a thin protector plate under butt of panel. Raise butt with a claw hammer on each side of tab when forming tab back in by hand. Do the final tuck with a narrow non-marring tool.